Simcenter 3D
Simcenter 3D
Simcenter’s integrated high-end multidisciplinary solutions can be expanded for use by CAE analysts and subject experts.
ABOUT software
Simcenter allows you to predict the performance of designs based on 3D geometry. In our Simcenter 3D CAE product, you can import geometry from any CAD source, and you can prepare it for multiple CAE methods (including finite element, boundary element, computational fluid dynamics, and multibody dynamics) in a unified environment ) Analysis model.
Simcenter’s integrated high-end multidisciplinary solutions can be expanded for use by CAE analysts and subject experts. In addition, by linking 3D simulation to Simcenter’s 1D and testing solutions, you can achieve unparalleled accuracy.

The most advanced, fast and accurate solver for linear finite element, nonlinear finite element, boundary element, multi-body dynamics, fatigue, thermal calculation and CFD calculation
In the modern CAE software market, it has the best geometric editing capabilities and associated simulation modeling capabilities compared with other similar software
Simcenter 3D provides specialized solutions and pre/post processing methods for structure, NVH and acoustics, heat flow, composite materials, motion, rotor dynamics, durability, optimization and multiphysics
Simcenter 3D has dedicated solutions related to test data, as well as co-simulation capabilities with 1D and control models
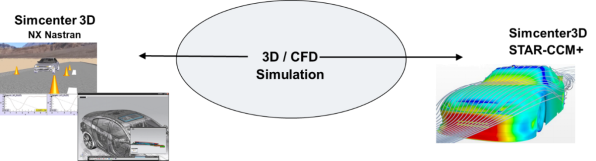
1. Structural simulation 2. Acoustic simulation 3. Mechanism movement 4. Composite materials
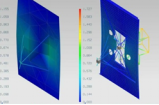
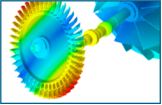
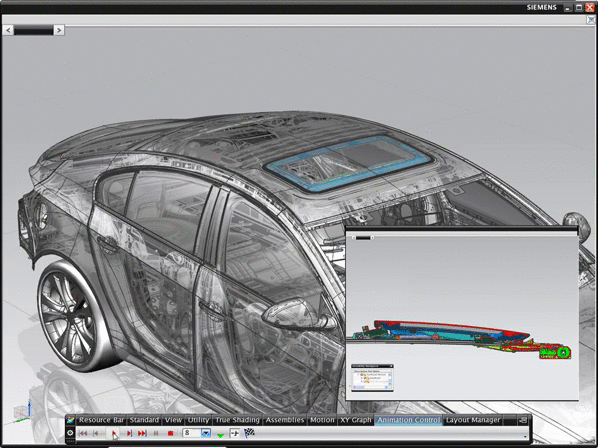
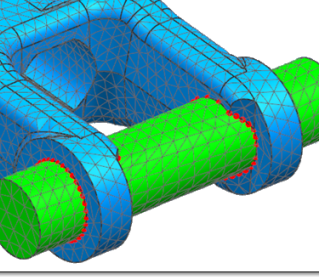
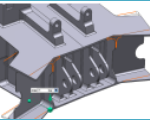
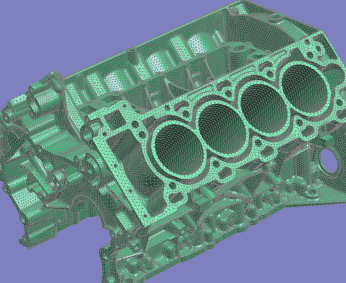
The main function
Used for structural strength analysis, dynamic response analysis and nonlinear analysis, vibration analysis, fatigue durability analysis, heat-fluid coupling analysis, space orbit parameter analysis, etc. The main functional modules are as follows:
Simcenter 3D
- Structural static analysis (linear/nonlinear)
- Modal analysis (natural modal analysis, prestressed modal analysis, complex modal, comprehensive modal analysis)
- Transient dynamic analysis (linear/nonlinear, multiple algorithms, various damping)
- Harmonic response analysis (multiple algorithms, considering the influence of prestress and damping)
- Response spectrum and random vibration analysis (single/multipoint response spectrum, single/multipoint PSD spectrum, DDAM response spectrum)
- Topology optimization analysis and calculation can guide the additive manufacturing process
- Fatigue calculation, carry out structural life prediction analysis
- Structural movement simulation, capable of carrying out structural movement analysis directly based on the design model
- Able to carry out heat flow simulation and provide various simulation calculation methods, including space orbit parameter simulation calculation
- Open material library (users can expand and modify)
- Fully WINDOWS style graphical user interface, management model objects based on project management
- Possess geometric modeling capabilities and CAD graphics interface
- With direct modeling technology, identification of no parameter model modification